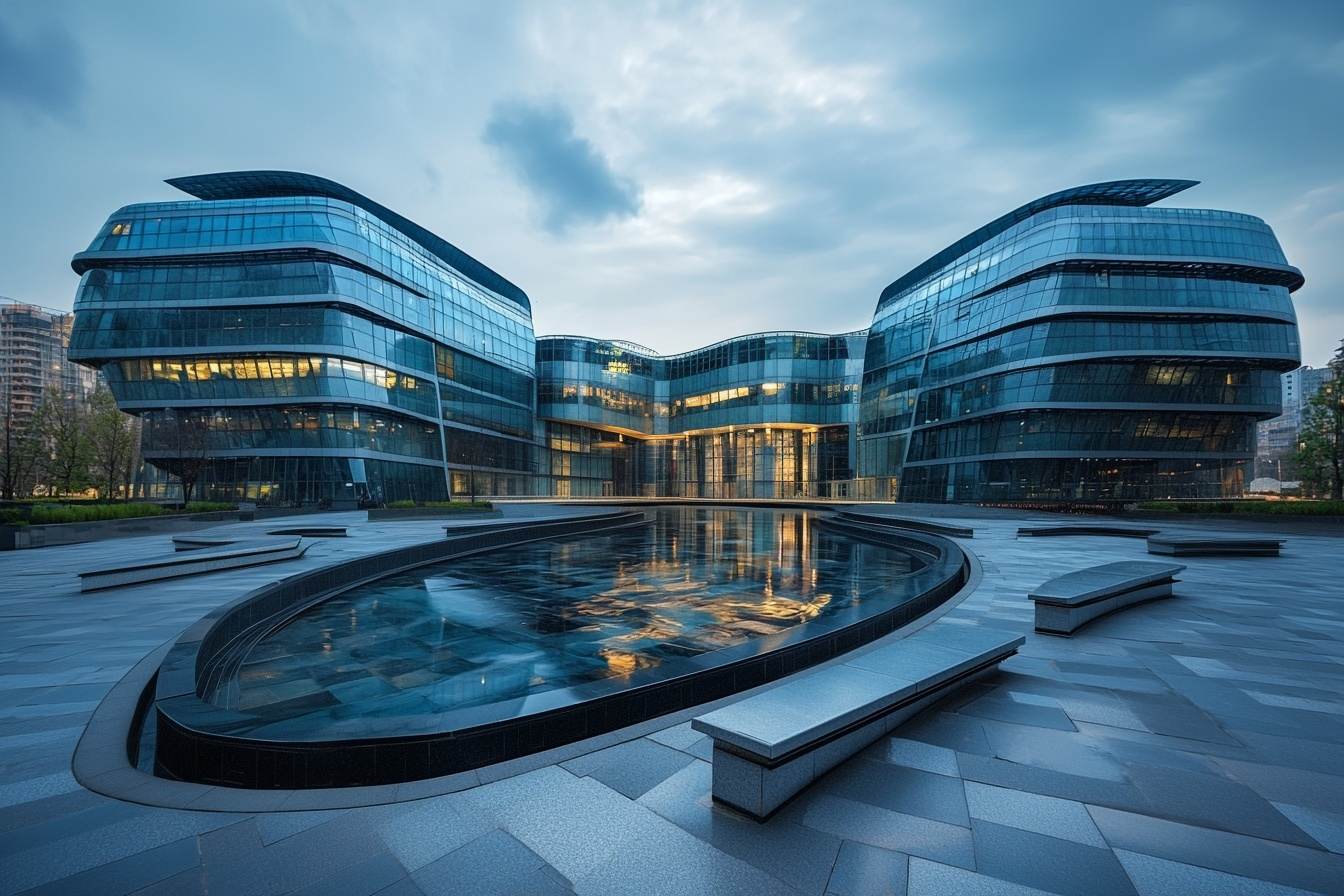
Financial Framework
A comprehensive financial framework designed for productized real estate delivery, providing a structured approach to investment planning, cost analysis, and return projections across the entire asset lifecycle.
Introduction to the I5 Financial Framework
The I5 Model requires a structured approach to investment planning, cost analysis, and return projections that differs significantly from traditional methods. This framework provides practical guidance for establishing a robust financial foundation that supports productized real estate delivery, specifically accounting for the owner's investment in core digital platforms like the Body of Knowledge (BoK), Virtual Showroom (VS), Design for Manufacture and Assembly (DfMA), and Architecture, Engineering, and Construction (AEC) platforms, as well as their associated operational costs.
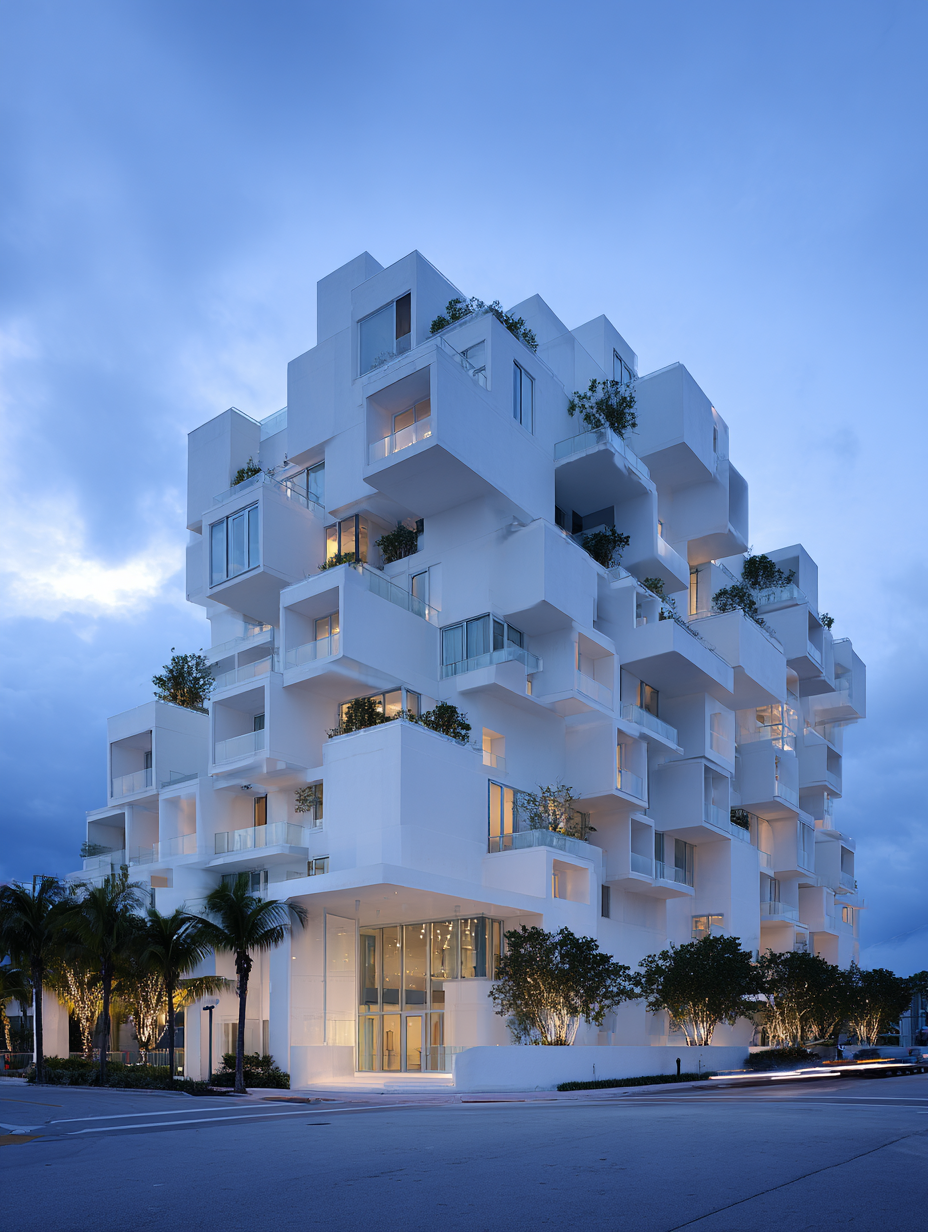
Key Differences from Traditional Financial Frameworks
Owner Digital Platform Investment
Unlike traditional models with minimal or no platform investment, I5 involves significant upfront and ongoing investment in owner-controlled digital platforms for their procurement, creation, customization, integration, administration, maintenance, and updates. These costs are often amortized across a portfolio or programs, rather than per project.
Design & Engineering Costs
Traditional approaches have sequential design and engineering costs, typically 3-5% of total project cost. In the I5 Model, these costs are front-loaded and higher (5-7%) due to increased initial investment to enable standardization and Design for Manufacture and Assembly (DfMA), with these design costs then amortized across multiple projects.
Shift to Off-site Manufacturing
I5 significantly shifts a portion of construction costs (25-35%) to factory production of standardized components in partner facilities. This contrasts with minimal or no off-site manufacturing in traditional models.
Reduced On-site Construction
On-site costs are reduced to 35-45% of the total, focusing primarily on assembly and integration rather than raw material construction.
Lower Contingency
Due to reduced variability from standardization, the I5 Model typically requires a lower contingency (3-5%) compared to the 5-10% seen in traditional methods, although technology-related risks must still be considered.
Compressed Financing Costs
Shorter delivery cycles lead to reduced financing costs (3-6%) through faster project completion.
Benefits of the I5 Financial Framework
Schedule Compression
Timeline reduction and 1-3% cost savings from reduced financing costs through parallel processing and off-site manufacturing.
Quality Improvement
Reduction in defects and 1-2% savings in warranty costs due to controlled manufacturing environments and standardized designs.
Cost Efficiency
Direct cost savings across multiple projects through material waste reduction, labor productivity improvements, economies of scale, and reduced design costs via reuse.
Sustainability Enhancement
Waste reduction and 20-30% embodied carbon reduction through optimized design and factory production.
Scalability Benefits
Increase in delivery capacity with the same resources by supporting the delivery of multiple projects with consistent quality and predictable outcomes.
Platform Efficiency Gains
Investing in and utilizing the owner-controlled BoK, VS, DfMA, and AEC platforms leads to improved collaboration, reduced errors, faster decision-making, and better knowledge management.